TasWater managing diverse infrastructure set on a dispersed island
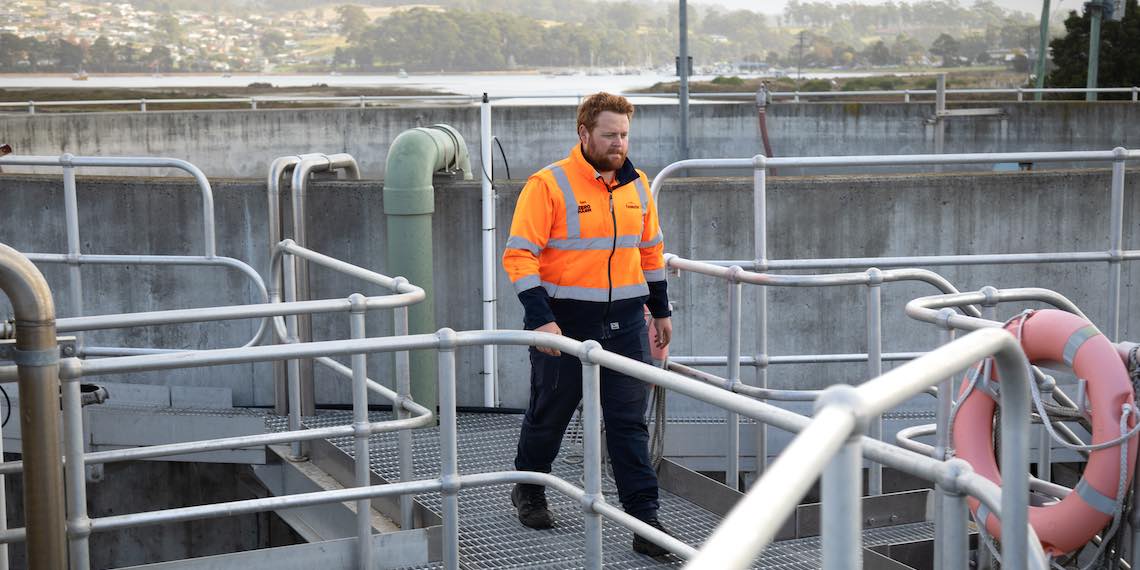
It has been eight years since TasWater formed from the merger of three regional utilities and inherited an extraordinary array of assets, previously managed by 29 different councils, dispersed across the state. As part of the Water Source asset management series, we spoke to the Australian Water Association Asset Management Specialist Committee member Mark Rippon, Treatment and Pumping Asset Performance Manager, to discuss how TasWater approached the challenge of managing such a large inheritance.
“When TasWater formed in 2013, we received 220,000 service connections across the state, servicing 80 per cent of the population of Tasmania,” Rippon said.
“Today, we’ve got 61 drinking water systems, serviced by 61 separate water treatment plants. We also have an additional 19 re-chlorination stations in the network, nearly 6500 km of water mains and roughly 292 storage facilities, dams and reservoirs.
“In addition, we have a combination of water and sewage pump stations, approximately 750 sewage pump stations and about 220 water pump stations. We’ve also got almost 187,000 sewage connections, which are serviced by 4800km of sewage mains.”
Rippon said TasWater’s asset profile is a result of the dispersed population in Tasmania.
"Historically, council’s managed their services, which resulted in disparities in asset management strategies throughout the state,” he said.
“Our customers are located in three major clusters — Hobart, Launceston and Devonport — and the rest of the population is scattered, just like the infrastructure. The number of assets we have makes our job challenging.”
Meeting the challenge
“This challenge is big, when you compare us to a utility like Sydney Water, who have concentrated infrastructure that services a much bigger population,” Rippon said.
“They have 16 sewage treatment plants for 5.2 million people, and we have 110 wastewater plants for a population of 500,000.”
TasWater has approximately 2-3% of the revenue base of all the water utilities across Australia, but has about 38% of the infrastructure facilities, Rippon said.
“Some of our plants are in great condition, but that can't be said for everything,” he said.
“We have to work hard to keep on top of urgent matters, while being innovative and applying what we learn from other utilities more advanced in their asset management maturity.”
Embracing digitisation
Rippon said that in the last eight years, TasWater has made some big strides in joining these disparate systems into one way of working.
“There have been teething issues but we’ve made a lot of progress. We’ve gone for a statewide approach and worked proactively with our customers to listen and understand their needs,” he said.
“We have assessed our infrastructure in terms of importance in achieving our promises to our customers and have been able to invest so we can deliver compliance upgrades, improvements and renew infrastructure to continue to meet our customers’ expectations.
“But we’ve also progressed in digitising our asset management plans and implementing Maximo as our enterprise asset management system. This allows us to identify the gaps in our data knowledge and look for ways we can improve it to better support our asset management decision making.”
Rippon said the utility is still in the process of bringing all of its assets onto a central SCADA — supervisory control and data acquisition — platform, as the three original utilities operated with different systems. Consolidation to a single platform will allow TasWater to implement its operational information systems (OIS) strategy and engage in opportunities around the industrial internet of things.
“We’ve got an operational centre (OC), but it needed three different SCADA systems open to analyse alarms for assets across the state,” he said.
“Furthermore, we have a customer management tool, called Gentrack. We also used to have three instances of this software. We’ve wound right back on these multiplications to drive efficiency and ensure we can use these systems more effectively.
“We are now moving to a place where our management plans are digitised and aligned with our data sources in one central location, to make sure we have one source of truth.”
TasWater has been using tools like Power BI to create better insights from information, Rippon said.
“We also put in place our enterprise time-series data historian, which is a tool to help us use analytics across multiple systems and sites to help identify and predict asset failure,” he said.
Reliability-centred focus
In addition to focusing on refining systems and digitisation, TasWater has also undergone a transformation in terms of its approach to asset failure.
“Our customers rightly expect a reliable service at a reasonable price. We started our reliability-centred journey about 15 months ago,” Rippon said.
“We identified that our preventative maintenance program was not targeted and was not giving our operators the time, the tools and the process required to deliver effective maintenance.
“Transitioning to a reliability-centred system has seen the development of equipment maintenance strategies that align the way a piece of infrastructure fails, to a preventative maintenance intervention program.
“This means we focus on increasing reliability or performance of the asset, and in conjunction, a potential reduction in operational costs for the business.”
Additionally, TasWater is also starting to analyse the secondary actions from its preventative maintenance activities.
“We can identify whether we need to incorporate additional tasks into the regular maintenance functions, or if we can extend the frequency of our maintenance intervention because the asset is performing well,” Rippon said.
“The reliability-centred program is also focused on defect elimination for infrastructure failures, and not accepting that failures are okay.
“We use a number of triggers that identify the need to do a root-cause analysis or escalate to a detailed incident cause analysis method investigation.
“Then we assess the way the infrastructure failed and try to implement interventions to prevent the failure from occurring again. We do this through capital interventions, modifications to existing PM programs or implementation of condition-based monitoring programs.
“We want to make sure that all the work we are asking our people to do has an important reason, it’s a real balancing act.”
Next steps
While TasWater has come a long way in creating more effective processes around the management of its huge asset profile, Rippon said there’s still work to do.
“We’ve got a big focus in the next few years to develop our system master plans and strategies so that we know what our infrastructure needs to look like in the next 30 years,” he said.
“From a work management perspective, we are developing and building a robust planning and scheduling function that will improve the quality and efficiency of our work within the field.
“This will help to improve the efficiency of our capital works program and decision making so we can stay focused on building and maintaining the infrastructure Tasmania needs to cope with future demands.”